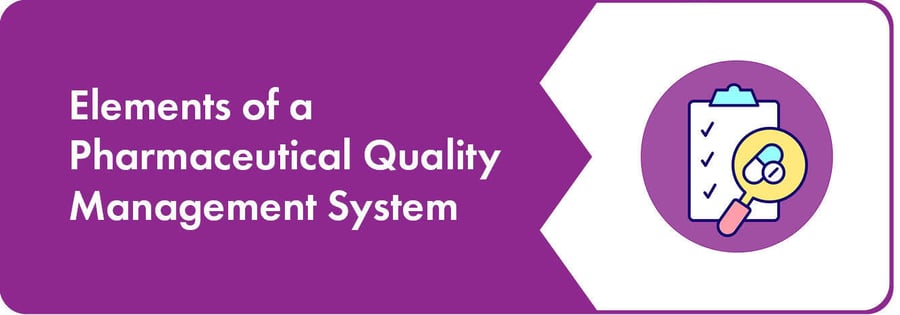
Elements of a Pharmaceutical Quality Management System
August 15, 2024
Pharmaceutical companies must have a pharmaceutical Quality Management System (QMS) to meet regulatory compliance obligations and ensure product quality. QMS software helps pharmaceutical manufacturers detect and correct errors, avoiding larger problems, such as a mandated recall. Additionally, QMS software enables companies to maintain and improve overall quality and efficiency.
QMS software helps keep products safe and effective while meeting regulatory requirements for FDA 21 CFR Parts 210 and 211 along with ICH Q10. QMS applications, such as document control, audit management, employee training and management review, along with quality metrics, are essential to maintaining strong quality standards.
Monitoring and reviewing quality processes helps companies proactively identify potential issues and risks. Quality metrics are used to measure and track the effectiveness of quality processes and identify areas for improvement. Let’s explore the key elements of a pharmaceutical quality management system.
What is a pharmaceutical quality management system?
In simple terms, a pharmaceutical quality management system is a collection of procedures, processes and policies designed to maintain and ensure uniformity and high quality during the production of pharmaceutical products. The system must reflect all applicable regulatory requirements.
A pharmaceutical quality management system addresses all drug manufacturing stages, including:
- Method Development
- Production
- Facilities and Equipment
- Materials Management
- Laboratory Controls
- Packaging and Labeling
Elements of a pharmaceutical quality management system
Document Control
One of the foremost elements of a pharmaceutical quality management system is document control, which systematically maintains, tracks and stores all documentation. Document control applications can help create, revise and route for review and approval, documents such as standard operating procedures (SOPs), records and protocols, allowing companies to easily maintain compliance with standards and regulations.
By implementing document control applications, pharmaceutical companies can easily track document changes to ensure that the correct version is always available to be used. Robust documentation encourages transparency and accountability since all changes and approvals are well documented and tracked.
Customer Focus
A customer-centric approach to pharmaceutical development and manufacture encourages employees to focus on end-user satisfaction and health. With customers front of mind, quality becomes a part of every step in pharmaceutical creation and delivery. This focus helps increase market share by building brand loyalty and awareness.
Regulatory Compliance
Pharmaceutical companies must comply with national and international standards and regulations, such as current Good Manufacturing Practice (cGMP), FDA regulations and international standards, such as ISO 17025. By adhering to these regulations, pharmaceutical companies can ensure that their products are effective and safe. Failure to comply with industry regulations can lead to severe consequences, penalties, damage to the company's reputation and fines. Pharmaceutical companies must stay up to date on requirements and make adjustments in their quality management system whenever necessary.
Risk Management
Every pharmaceutical company must have structured risk management guidelines to help identify, assess and mitigate quality risks. This approach allows companies to address possible risks before they escalate. Risk management involves quality checks at regular intervals and implementing corrective measures.
Through evaluation, pharmaceutical manufacturers can implement measures to reduce errors and defects. This process also helps maintain product quality according to standardized regulatory requirements.
The risk management process can also help identify and address potential risks in a company’s supply chain. By assessing the supplier's vulnerability, manufacturers can devise plans to mitigate risks, thus helping build strong relationships with suppliers and ensuring any disruption to operations.
Training & Competencies
Regular training is required for employees working at all points in pharmaceutical development, production and distribution processes to ensure they have the knowledge and skills necessary to perform their jobs effectively and maintain the highest levels of quality and safety. Regular assessment programs must be conducted to evaluate the competency of employees and locate any areas for improvement. Records of employee competence and training completion are essential.
Roadmap to the success of a quality management system
The success of a pharmaceutical quality management system is critical to ensuring the safety and efficacy of medications. One of the first steps that should be undertaken is to define quality objectives, then set measurable and attainable goals. Goals should provide a roadmap that enables your company to easily align with quality standards.
Quality standards and procedures should establish responsibilities for each department and individual within the organization. This guides teams towards the same goals and achieves consistency in a systematic manner.
It is vital to monitor quality systems and processes at regular intervals to ensure their effectiveness. Regular audits and inspections are necessary to identify areas for improvement. By adhering to a roadmap, companies can have a robust quality management system that meets all regulatory requirements.
Conclusion
A successful pharmaceutical quality management system is necessary for pharmaceutical companies to ensure product quality, regulatory compliance and customer satisfaction. By adhering to these elements, companies can not only prevent inefficiency but also enhance product quality. A well-designed system will increase customer satisfaction, trust and confidence in your brand.
Related Content
• Pharmaceutical QMS
• Pharmaceutical Quality Assistance
• Document Control