1,000+ customers worldwide
Ensure Consistent Quality
Create a culture of continuous improvement with a robust set of integrations that enable you to drive productive workflows.
- Employee Training: Assign, monitor and follow up on employee training
- Inspection Plans: Create inspection plans, track details and seamlessly escalate if necessary
- CAPAs and NCPs: Automate corrective actions and nonconforming products events
- Supplier & Customer Portals: Manage supplier and customer communication and data, and link with corrective actions
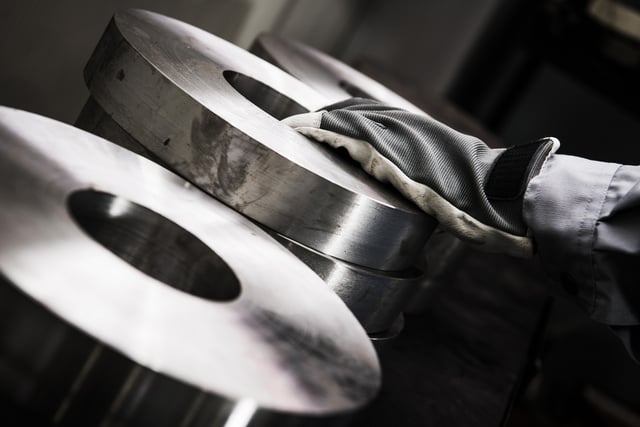
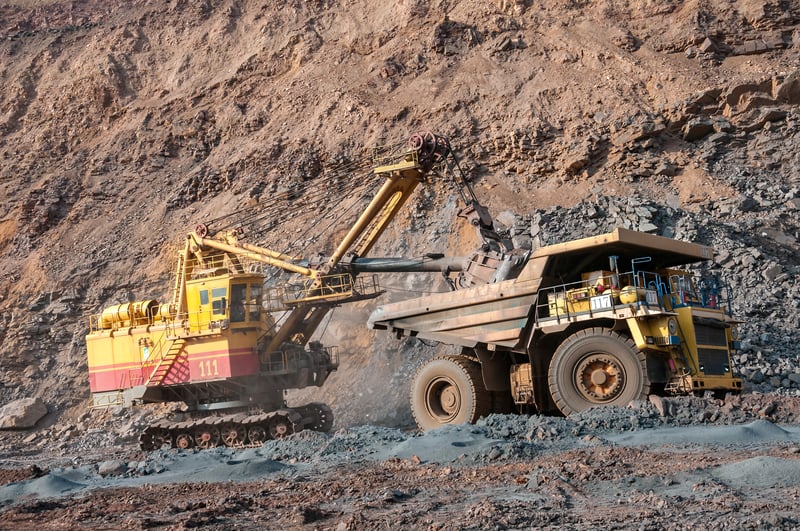
Mitigate Risk and Reduce Audit Pain
Reduce the chance for human error with electronic records and easily monitor, track and report on risk assessment tasks.
- Electronic Approvals: Electronically assign approvers and approve, reject or verify risk assessments
- Real-Time Data: Mine real-time data to analyze trends
- Automate Task Management: Set up email alerts, export and email copies of risk assessments, attach unlimited files as needed
Track and Manage Safety
All safety incidences are managed electronically from start to resolution. Easily document and analyze safety incidents, identify trends and integrate to corrective actions.
- Automatic Alerts: Major injury reports trigger admin alerts in compliance with OSHA guidelines
- Electronic Tracking: Track injury types and related data and get real-time status and analytics
- User-Defined Fields: Create unlimited custom fields for tracking company-specific information
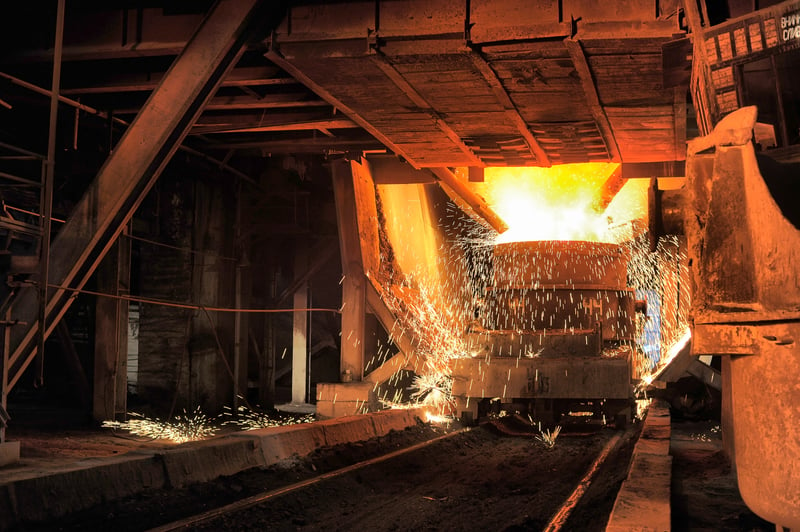
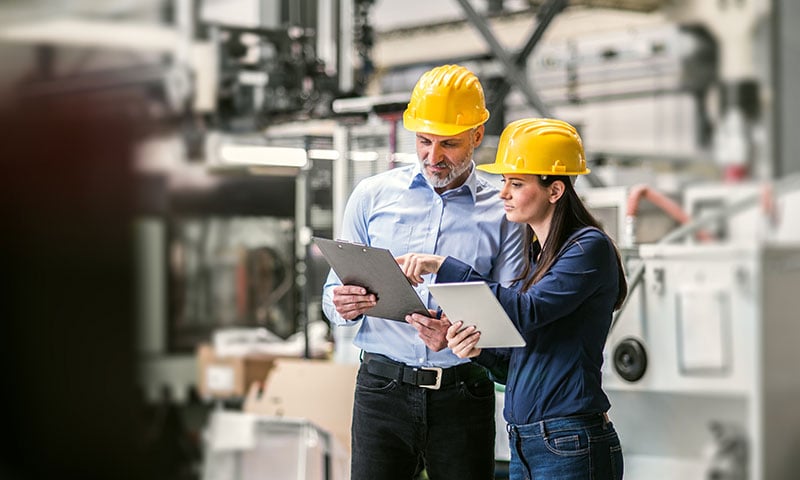
Centralize ISO 9001 Compliance
Digitally transform your organization by unifying information and compliance processes with connected modules. Link all of your quality compliance information together and replace spreadsheets.
- Risk Assessment Module: Manage risks by assigning actions, risk scores, tasks, priorities and employees to minimize potential issues
- Calibration Module: keep track of your company's measurable equipment and maintain calibration records
- Document Control Module: See your documentation all in one place. Link data across locations, departments, employees, suppliers and customers
Frequently Asked Questions: Metals and Mining QMS
What are quality management regulations for the metals and mining industry?
The nature of quality and compliance tasks in the metals and mining industry varies relative to the stage of discovery or production in which a company is working. Metals and mining companies generally adhere to guidelines put forth by the International Organisation for Standardization (ISO): ISO 9001, which outlines optimal standards for establishing a quality management system; ISO 14001, which addresses environmental management systems; and ISO 45001, which establishes occupational health and safety management guidelines.
Why is quality important in the metals and mining industry?
Ensuring the quality of metals and mining products and services means delivering consistent and reliable materials to customers. This is especially important in industries that rely on quality metals materials to ensure the safety and quality of their own products, such as in the aerospace, automotive or construction industries.
In addition, having a robust quality management system improves operational efficiency, reducing waste, minimizing rework, increasing productivity and positively impacting the bottom line.
What quality management tasks affect the metals and mining industry?
Some of the most common tasks addressed by a quality management system in the metals and mining industry include:
- Document Control
- Inspection Management
- Regulatory Compliance
- Safety Management
- Employee Training
- Supplier Management
- Equipment and Instrument Calibration
- Continuous Improvement
How can the metals and mining industry benefit from an eQMS?
Investing in quality management helps prevent financial losses and contributes to the long-term profitability of a company. Automating quality and compliance with an eQMS brings a host of efficiencies to metals and mining businesses, including:
- Easier collaboration
- Reduced costs
- Faster time to market
- Better brand reputation
- Customer satisfaction
- Multi-site operations visibility
- Real-time data for reporting and analysis
- Simplified compliance management
Why choose QT9 QMS to automate your quality management tasks?
With more than 25 modules that come standard, QT9 QMS excels at all of the processes metals and mining companies need for managing quality, including:
- Document Control
- Risk Management
- Audit Management
- Corrective Actions
- Supplier Management
- Employee Training
- Inspections
- Safety Incidents
QT9 QMS is a highly rated, easy-to-use and affordable quality management system based in the cloud for ultimate collaboration and connection. QT9 QMS offers unlimited scalability and traceability, full customer support, an ERP integration and Business Intelligence tool to help visualize and make informed decisions using real-time data.
QT9™ QMS is flexible for your business.
QT9 lets you choose modules based on what's best for your organization.
Modules for any business size
With multiple modules to choose from, there's solutions for nearly anyone.
A solution that scales with you
Whether you are a large corporation or a small start-up you can use as many modules as you want.
Cross-Platform Support
Whether you use Android, iOS or Windows, QT9 works from virtually any web browser.