Orbion Space Technology Centralizes AS9100 Compliance
Orbion’s investment in a centralized QMS ensures their quality processes are as forward-thinking and precise as the technology they send into orbit.
Industry
Aerospace - Satellite
Founded
2016
Location
Houghton, MI
Employees
50+
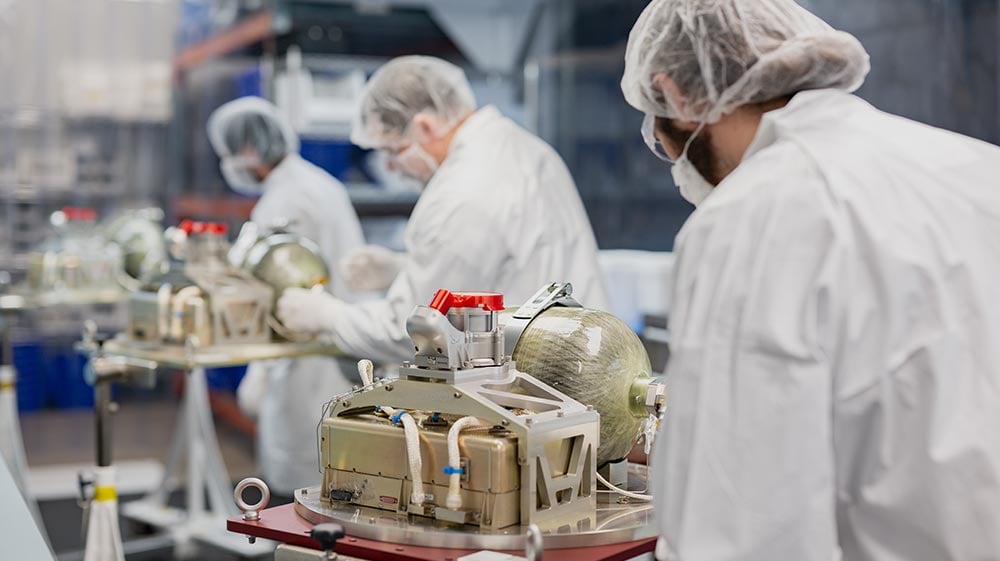
“Keeping track of correct approvals of documents, revisions and proper templating used to be a full-time job”.
- Rebecca Kopke
Quality Manager
Orbion Space Technology Case Study
Obion Space Technology is an innovative aerospace startup based in Michigan’s upper peninsula. The company is the developer and manufacturer of unique, plasma-based thrusters used to propel satellites.
Orbion’s signature product, the Aurora Hall-Effect Propulsion System, uses this electrically charged propellent to maneuver satellites after they have been ferried into space on another rocket. Its revolutionary systems are lighter and more fuel-efficient than the standard, with the ability to maneuver away from potential hazards and return to earth in a more controlled manner.
Orbion has also created a proprietary manufacturing process that increases output capacity and lowers the cost of producing these thrusters without sacrificing reliability. Their combination of robotic and “touch” assembly is revolutionizing satellite availability amidst a surge in demand for the technology.
Revolutionizing quality management
It’s rocket science at its finest. But even if you’re a company with rocket scientists leading the charge, when you’re a startup answering to investors, you need to be especially strategic about where and how capital is used.
That’s why when Orbion decided to upgrade its quality processes, it was incumbent upon their team to search for a quality management system that could provide a comprehensive software solution that meets the company’s quality and compliance needs in the most efficient, affordable way possible.
After evaluating competitors in the aerospace eQMS market, Orbion chose QT9 QMS based largely on the breadth and depth of its applications, flexible license structure and robust provider support.
Orbion implemented QT9 QMS two years ago. Now the company saves 10-15 hours of manpower per week and continues to reap the benefits of QT9’s centralized, automated and integrated quality management system software.
“Most of our time savings comes from automating documentation and not having to track down answers to technical questions and issues,” says Rebecca Kopke, Quality Manager at Orbion. The QT9 QMS system “allows us to quickly access any information pertaining to our quality processes.”
AS9100 compliance
Orbion is an AS9100-certified company. As such it is subject to more rigorous regulatory requirements than many industries. These include:
-
Additional production and operations controls
-
More in-depth risk identification and assessment
-
A dedicated QMS management representative
-
Deeper employee involvement in total quality
-
Expanded nonconformance actions
-
Close control of external resources
-
Specific design and development testing and validation
The QT9 QMS Audit Management module helps Orbion meet these expectations, creating efficient workflows and giving them the means to more easily demonstrate to auditors how they are meeting AS9100, as well as ISO, requirements.
With the Audit Management module, the Orbion team can create individual audits as well as assign action items and to-do lists directly from the module without having to manually email or track down process owners.
“All audits are found in one place, and users can address them the same way with the same process every time,” says Kopke. “It shows our company and our auditors that we have repeatable processes in place that are followed by each department.”
Nonconformance management
Among the first tasks Orbion wanted to address with new QMS software was centralizing its nonconformance processes. “Noncentralized nonconformance processes spread across multiple spreadsheets had become extremely time-consuming to manage,” says Kopke.
With use of QT9 QMS, Orbion has seen average times to closure for nonconformances decrease and process efficiency improve. Nonconformance urgency is more visible and documentation and approvals more efficient due to streamlined, centralized processes.
Module integrations also play a role. With direct connections to other QT9 QMS modules, such as Deviations, CAPA Management and the Supplier Web Portal, Orbion is able to speed the nonconformance process.
Extracting nonconformance data has become easier with the new QMS system. Before QT9, extracting nonconformance metrics was time-consuming, taking days to manually gather and prepare data for reviews. “QT9 has significantly reduced the time to prepare for a management review session,” says Kopke. “Management Review preparation itself was multiple days to weeks to ensure the data was correct and compiled on time.”
QT9 QMS has simplified the process of extracting needed metrics, similar to how it has streamlined audit documentation. And with real-time data provided by a cloud-based eQMS, decision making can be more impactful.
Document control
Because document management is such an important part of consistent quality and key to meeting many compliance standards, it usually has a huge impact on organizations that move from disparate quality systems to one, centralized platform that manages all documentation tasks. The same has been true for Orbion.
“Keeping track of correct approvals of documents, revisions and proper templating used to be a full-time job,” says Kopke. “Official document locations varied by department, and every department had different processes for training documents or signature authority levels. Tracking down the latest correct versions of official documents was difficult.”
Today Orbion has a streamlined system for document management, and all documents are accessible via centralized QT9 QMS software. Cloud-based delivery provides real-time data, so employees are always working from the most current documentation. Automated approval workflows ensure documentation revisions are controlled and communicated appropriately.
Involvement and agility
Orbion uses more than half of QT9 QMS’s 25+ modules, with document control, audit management, nonconforming products, deviations, corrective and preventive actions, and quality events modules offering the most notable benefits.
Some unexpected benefits of implementing QT9 QMS have been seen as well. Particularly in the increased involvement of Orbion team members in the quality management process. This is fostered, not just from centralized, integrated applications, but from overall increased visibility into the entire quality picture.
Centralized applications, combined with the ability to assign tasks to process owners through the QT9 QMS “To-Do List,” support the company’s push to engage all employees in regulatory activities and creates efficiencies for the quality team that indirectly impact the bottom line.
“The To-Do lists spread accountability to individuals and keeps the Quality Department from having to follow up on every single aspect of the QMS process,” says Kopke. Accordingly, the quality team is able to focus on more value-added activities.
For Orbion, this means that coordination between departments such as manufacturing and engineering has improved, especially as they scale up use of the QMS's ISO modules, such as Nonconforming Products, Deviations, CAPA Management and Quality Events.
Conclusion
Orbion Space Technology’s journey to streamline and centralize its quality management processes has delivered measurable results. By implementing QT9 QMS, the company has not only simplified its AS9100 compliance but also unlocked efficiencies that save hours of manpower each week—time that can be reinvested into innovation and growth.
As they continue to scale production of their groundbreaking propulsion systems, Orbion’s investment in a centralized QMS ensures their quality processes are as forward-thinking and precise as the technology they send into orbit.
Challenge
Streamlining and centralizing quality processes and data, creating efficiencies and organization.
Solution
An affordable QMS that offers end-to-end capabilities to support AS9100 certification.
Results
Save 10-15 hours of manpower per week, which can be devoted to more value-added tasks.About Swagelok
Obion Space Technology is an innovative aerospace startup based in Michigan’s upper peninsula. The company is the developer and manufacturer of unique, plasma-based thrusters used to propel satellites.
Orbion’s signature product, the Aurora Hall-Effect Propulsion System, uses this electrically charged propellent to maneuver satellites after they have been ferried into space on another rocket. Its revolutionary systems are lighter and more fuel-efficient than the standard, with the ability to maneuver away from potential hazards and return to earth in a more controlled manner.
“The QT9 QMS system allows us to quickly access any information pertaining to our quality processes.”
- Rebecca Kopke
Quality Manager